Chinese Cloisonné — Jingtai Blue
By staff reporter XING WEN
WHEN visiting the Forbidden City, the Summer Palace or any former imperial residence, one can always find beautiful Chinese cloisonné wares on display. Such crafts, made with red copper, are also known as Jingtai Blue. Making the distinctive objects is a comprehensive and sophisticated process, an integration of foreign enamel techniques, traditional Chinese bronze and porcelain making, as well as traditional painting and etching skills.
The Humblest and Grandest Admirers
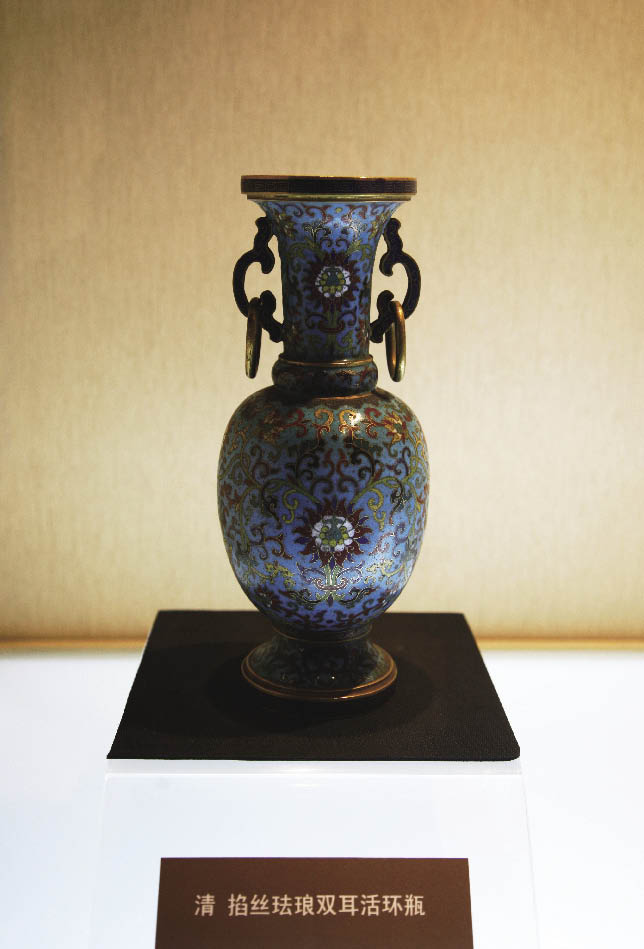 |
Cloisonné vase of the Qing Dynasty. |
Cloisonné was a symbol of nobility and wealth in the Ming (1368-1644) and Qing (1644-1911) dynasties and was supplied exclusively to the royalty in these times. It took radical political change for the technique and its products to become available to commoners.
Beijing was the cradle of this complex handicraft. It is believed that the enameling technique reached China through missionaries from Central Asia sometime in the late Yuan Dynasty (1271-1368). Shortly after its introduction, the Chinese made cloisonné enameling a distinctive art form by mastering the skill of bronze casting and the glazing techniques in which artisans had to accurately control the firing temperature. Products of this period are modeled on the elegant porcelain style of the Song Dynasty (960-1279).
The technique came into its heyday during the reign of Emperor Jingtai (1450-1456) in the Ming Dynasty. Craftsmen of this period substantially improved the coloring skill and found a sapphirine pigment that gave the products a certain class and solemnity in tune with the Oriental aesthetic. People dubbed it Jingtai Blue. Although various colors of enamels were perfected later on, blue remained the dominant color of the works. Gradually, Jingtai Blue replaced cloisonné as the referent for this kind of craft.
During the reigns of Qing emperors Kangxi and Qianlong, the Jingtai Blue manufacturing technique reached its zenith. Colors were more delicate, filigrees more flexible and fluent, and the products made from it included almost every kind of daily necessity. Snuff bottles, incense burners, chopsticks and bowls were common, but the best Jingtai Blue works produced during this mature period included even furniture.
A Jingtai Blue workshop was set up in the Forbidden City during the Qing Dynasty, specializing in producing enamelware for the royal family. Common people had little access to Jingtai Blue until the late Qing Dynasty when the breakup of the imperial court ended with craftsmen being dismissed. Private workshops then began to emerge, and Jingtai Blue wares began to trickle into the general market.
Soft Fire Makes Sweet Malt
Producing Jingtai Blue is a highly complicated process. It starts with mold-making. Copper is easy to hammer and stretch, so is an ideal material to form the body of a cloisonné work. Craftsmen first choose pieces of copper of exactly the same thickness and then cut and hammer the pieces into molds for different utensils such as vases, jars, bowls, and plates. This framing step is the work of a coppersmith. However, once the body is shaped, the coppersmith's work is finished, and the cloisonné craftsman's task begins.
The second step of filigree soldering can be compared to embroidery, and is probably the most challenging step of the entire process, as it requires great patience and dexterity. With a blueprint in mind, the artisans make full use of their experience and imagination to cut and curve the copper filaments into various shapes such as flowers, birds, mountains and rivers. Sometimes, a single vase needs a 500-meter-long copper strip to form all the delicate patterns. Dipped in glue, the strips are then pasted onto the mold.
Now comes the enamel – the colorful overcoat for the cloisonné mold. Mineral ores for the pigments are ground and mixed with water. Usually the ore containing iron will turn gray, that containing uranium will go yellow, and chromium based ores green. Craftsmen fill in the lattices with these various pigments.
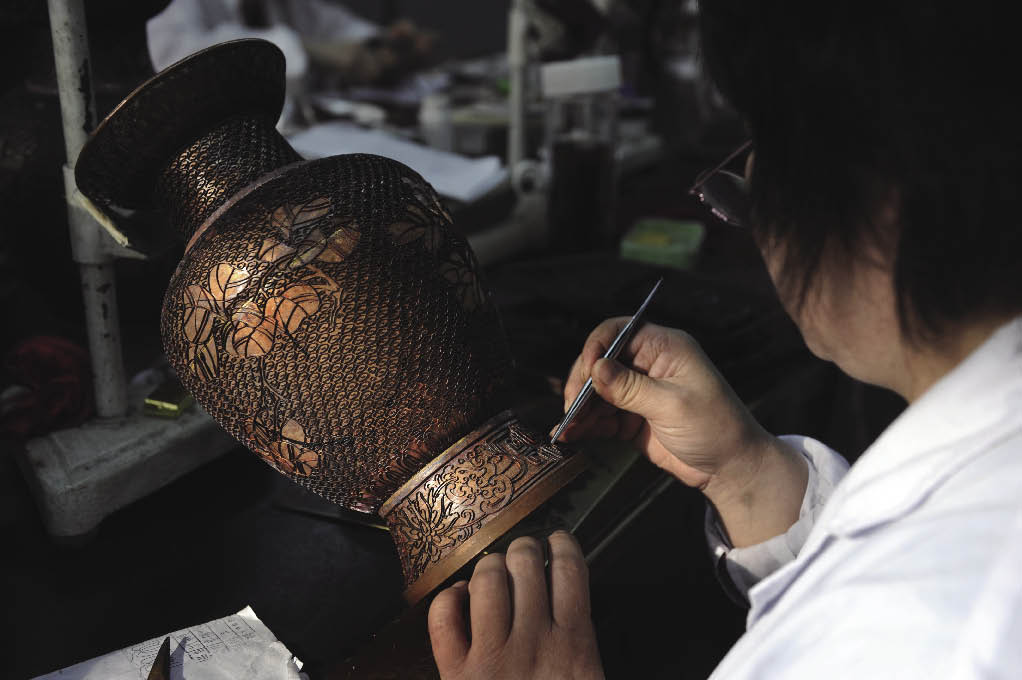 |
Filigree soldering can be compared to embroidery as it requires great patience and dexterity. |
|